The Ultimate Guide to Plastic Injection Mold in Metal Fabrication
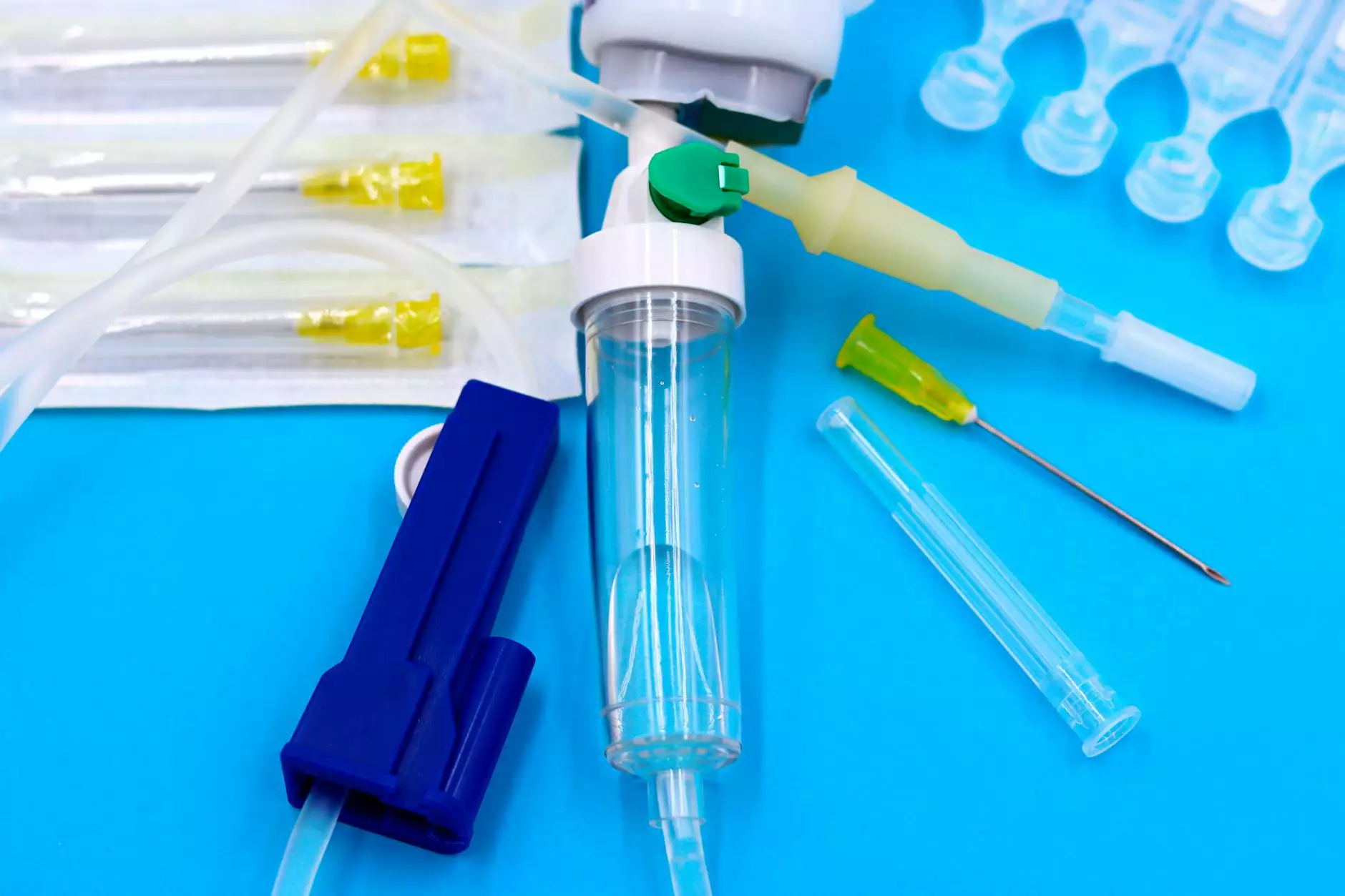
Plastic injection mold technology is revolutionizing the manufacturing landscape, especially within the metal fabrication industry. This detailed article will explore the intricacies of plastic injection molding, its advantages, applications, and why it is a vital component in producing high-quality metal fabrications.
Understanding Plastic Injection Mold
At its core, plastic injection mold involves a process where molten plastic is injected into a mold to create specific shapes and designs. This method is not just efficient; it allows manufacturers to produce complex objects with remarkable precision and speed. The ability to create intricate shapes makes it a preferred choice for many industries, including automotive, consumer goods, and even technology.
The Plastic Injection Molding Process
The process of plastic injection molding can be broken down into several key stages:
- Designing the Mold: The first step is designing a mold that meets specific requirements. This process often involves using CAD software to create a 3D model.
- Creating the Mold: Once the design is finalized, the mold is manufactured, typically from steel or aluminum, to ensure durability and precision.
- Heating the Plastic: Plastic pellets are heated until they reach a molten state, allowing them to flow easily into the mold cavities.
- Injecting the Plastic: The molten plastic is injected into the mold at high pressure, ensuring that every detail is captured accurately.
- Cooling and Solidifying: After injection, the plastic cools and solidifies within the mold. This step is crucial for achieving the desired properties of the plastic product.
- Removing the Molded Part: Once cooled, the mold opens, and the finished product is ejected. Any excess plastic, known as flash, can be trimmed away.
The Benefits of Plastic Injection Mold
Utilizing plastic injection mold technology offers numerous advantages for businesses in the metal fabrication sector:
- High Efficiency: The ability to produce large quantities of parts quickly makes plastic injection molding one of the most efficient manufacturing processes available.
- Precision and Accuracy: Molds are designed to very tight tolerances, which results in parts that are consistent and precise, leading to reduced waste and better quality.
- Cost-Effectiveness: While the initial cost of creating molds can be high, the long-term savings from mass production and reduced scrap make it economically viable.
- Versatility: Plastic injection molding can accommodate a wide variety of materials, allowing manufacturers to select the right type of plastic for their specific needs.
- Complex Geometries: The process allows for the production of complex shapes that might be impossible or too costly to create using other manufacturing methods.
Applications of Plastic Injection Mold in Metal Fabrication
The applications of plastic injection mold in the metal fabrication industry are extensive. Here are a few notable examples:
1. Automotive Components
In the automotive industry, there is a constant demand for lightweight and durable parts. Plastic injection molding plays a vital role in producing components such as:
- Dashboard bezels
- Interior trims
- Light housings
These components benefit from the mold’s precision, ensuring a perfect fit and minimal waste during manufacturing.
2. Consumer Products
The consumer goods market has widely adopted plastic injection molding to create everyday products, including:
- Kitchenware
- Household items
- Electronics casings
This method allows for a vast array of designs and features while maintaining consistent quality across large production runs.
3. Medical Devices
Quality and precision are non-negotiable in the medical field. Plastic injection molding is crucial for manufacturing components such as:
- Drug delivery systems
- Diagnostic equipment housings
- Implants
This capability significantly enhances the reliability and functionality of medical devices.
The Importance of Quality in Plastic Injection Mold Manufacturing
Quality is paramount when it comes to plastic injection mold manufacturing. Poor-quality molds can lead to defective parts, increased production costs, and compromised safety. At DeepMould.net, stringent quality control measures are implemented throughout the manufacturing process to ensure that every mold meets the highest standards. Key aspects include:
- Material Selection: The right materials are chosen based on durability and performance requirements.
- Precision Machining: State-of-the-art machining techniques are employed for mold creation, ensuring exact specifications are met.
- Testing and Validation: After fabrication, molds undergo rigorous testing to verify their design and functionality.
The Future of Plastic Injection Mold Technology
The future of plastic injection mold technology appears promising, with advancements leading to even greater efficiency and sustainability in manufacturing. Here are some trends to watch:
1. Eco-Friendly Materials
With increasing environmental concerns, there is a growing trend towards the use of biodegradable and recycled plastics in injection molding processes.
2. Automation and Industry 4.0
Integrating automation and smart technologies into the injection molding process will enhance production efficiency, reduce costs, and improve the quality of molded parts.
3. Innovative Designs with 3D Printing
Combining 3D printing with traditional injection molding allows for rapid prototyping and more complex mold designs, further pushing the boundaries of what is possible in manufacturing.
Conclusion
In conclusion, plastic injection mold technology plays a crucial role in the metal fabrication industry, providing effective solutions for a variety of applications. Its benefits of efficiency, precision, and versatility make it a fundamental process for producing high-quality components across different sectors. At DeepMould.net, we commit to quality and innovation, ensuring our clients receive the best possible products to meet their manufacturing needs.
As the industry evolves, businesses that embrace these advancements and prioritize quality will not only thrive but also lead the way in shaping the future of manufacturing.