Exploring Concrete Batching Plants: The Backbone of Modern Construction
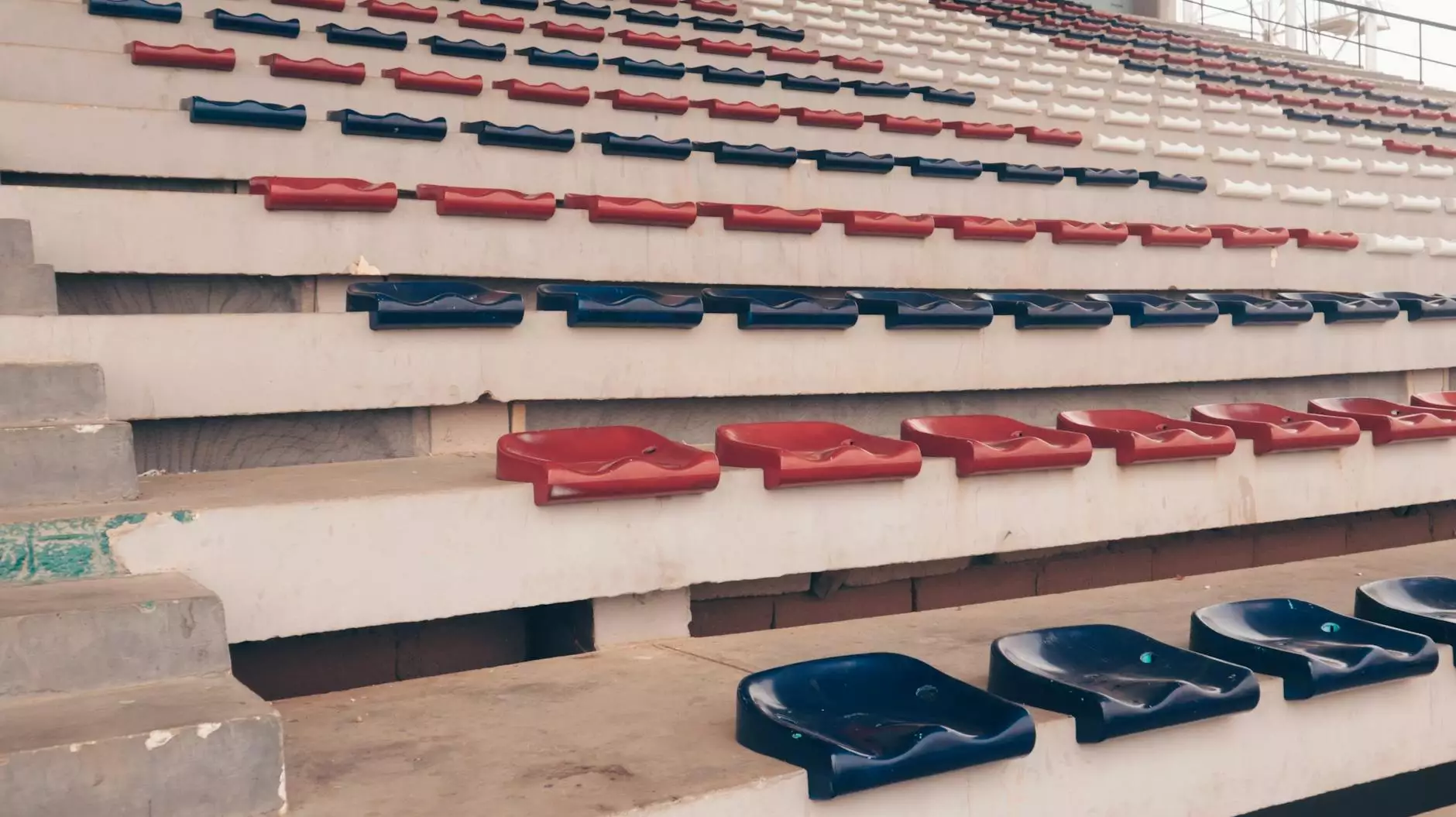
In today's rapidly evolving construction landscape, the concrete batching plant stands as a pivotal element in ensuring that high-quality concrete is produced efficiently and effectively. This comprehensive guide delves into the intricacies of concrete batching plants, highlighting their significance, components, operational processes, and the innovative technologies that shape the future of concrete production.
What is a Concrete Batching Plant?
A concrete batching plant is a facility that combines various ingredients to produce concrete. Ingredients include water, aggregates (sand, gravel, crushed stone), cement, and additives. These components are precisely measured and mixed to create concrete that meets specific project requirements.
The Importance of Concrete Batching Plants in Construction
- Quality Control: Concrete batching plants ensure consistent quality by meticulously controlling the batching process.
- Cost Efficiency: By optimizing material use and reducing waste, these plants can significantly lower production costs.
- Time Savings: Automated processes speed up the mixing of concrete, allowing for quicker delivery on job sites.
- Custom Formulations: Batching plants can produce various concrete types with predetermined properties suitable for different applications.
Components of a Concrete Batching Plant
The operational efficiency of a concrete batching plant depends on its various components, which include:
- Aggregate Bins: Storage units for coarse and fine aggregates, typically located at the top of the plant.
- Cement Silos: Used to store cement. They are designed to ensure a sealed environment to maintain quality.
- Mixers: Essential for blending the ingredients. They can be either pan, twin-shaft, or drum mixers, each serving specific needs.
- Weighing System: An integral component that measures the exact amount of each ingredient using load cells.
- Control Systems: Automated systems that monitor and control the batching process, ensuring precision and consistency.
- Discharge System: Ensures efficient delivery of the mixed concrete to trucks or directly on site.
Types of Concrete Batching Plants
Concrete batching plants come in various configurations, each designed to suit specific operational needs:
1. Stationary Concrete Batching Plant
This type is permanently sited in one location and is ideal for large-scale construction projects due to its efficiency and durability.
2. Mobile Concrete Batching Plant
These are transportable units that can be relocated to job sites as needed, offering flexibility and convenience for smaller projects.
3. Compact Concrete Batching Plant
Designed for smaller spaces, these plants offer limited output but maintain efficiency, making them great for urban projects.
Operational Process of a Concrete Batching Plant
The operation of a concrete batching plant involves several coordinated steps to produce high-quality concrete:
- Material Loading: Aggregates and cement are loaded into their respective storage bins, ready for batching.
- Weighing: The ingredients are precisely weighed according to the specified concrete recipe, ensuring accuracy and uniformity.
- Mixing: The weighed materials are transferred to the mixer, where they are thoroughly mixed to achieve a homogeneous material.
- Discharge: The finished concrete is then discharged into delivery trucks or directly loaded on site, ready for use.
Innovative Technologies in Concrete Batching Plants
As technology advances, concrete batching plants incorporate innovative features that enhance productivity and sustainability:
- Automated Systems: Modern plants utilize sophisticated software that automates the entire batching process, reducing human error and increasing efficiency.
- Environmental Controls: Many plants now implement measures to minimize dust emissions and recycle water, contributing to more sustainable construction practices.
- Telematics and IoT Integration: Features that allow for real-time monitoring and diagnostics, enabling predictive maintenance and reducing downtime.
Benefits of Using a Concrete Batching Plant
Concrete batching plants offer numerous benefits that are vital for successful construction projects:
- Improved Quality: The precision of the batching process results in higher quality concrete that meets required specifications.
- Increased Productivity: Quick and efficient mixing processes mean projects can proceed without delays linked to concrete supply.
- Customizable Mixes: Different projects require different concrete specs, and batching plants can easily adjust mixes to accommodate specific needs.
- Reduced Transportation Costs: On-site batching reduces the need for transporting ready-mix concrete over long distances.
Choosing the Right Concrete Batching Plant for Your Business
Selecting the appropriate concrete batching plant can significantly influence operational efficiency and project success. Consider the following factors:
- Project Size and Scope: Larger projects typically benefit from stationary plants, while smaller ventures may find mobile units more suitable.
- Production Capacity: Analyze your expected concrete demand to choose a batching plant that can meet production targets.
- Technological Features: Evaluate the automation level and control systems of the plant that enhances operational efficiency.
- Cost: Consider both upfront investment and long-term operational costs, including maintenance and labor.
Regulations and Compliance
Operating a concrete batching plant involves adherence to various regulations to ensure safety, environmental sustainability, and quality control:
- Environmental Regulations: Ensure compliance with local laws related to emissions, waste management, and noise control.
- Health and Safety Standards: Establish protocols for protecting workers during the operation, including proper training and protective equipment.
- Quality Assurance: Maintain standards for the concrete produced, as specified by local and international building codes.
Future Trends in Concrete Batching Technology
The concrete industry is continually evolving, and several trends are shaping its future:
- Smart Batching Plants: The integration of AI and machine learning to optimize batching processes and predict maintenance needs.
- Green Concrete: Increasing demand for eco-friendly alternatives that reduce carbon footprints in concrete production.
- 3D Printing: The advent of 3D printing technology in construction is influencing the development of new types of concrete mixtures.
Conclusion
In conclusion, the concrete batching plant is a fundamental component of modern construction, enabling the efficient production of high-quality concrete. Understanding its components, operational processes, and the latest trends in technology can provide businesses with a competitive edge in the construction sector. The future of concrete batching looks promising, with innovative solutions ensuring that the industry can meet the challenges of both quality and sustainability.